Cooling towers are essential for efficient heat management in industrial plants, commercial buildings, and HVAC systems. However, like any complex system, they are prone to various issues that can disrupt operations, increase energy consumption, and lead to costly repairs. The good news? Most common cooling tower problems can be prevented—or quickly fixed—with the right knowledge and proactive maintenance. In this guide, we’ll uncover the most frequent cooling tower problems and provide innovative solutions to keep your system running smoothly.
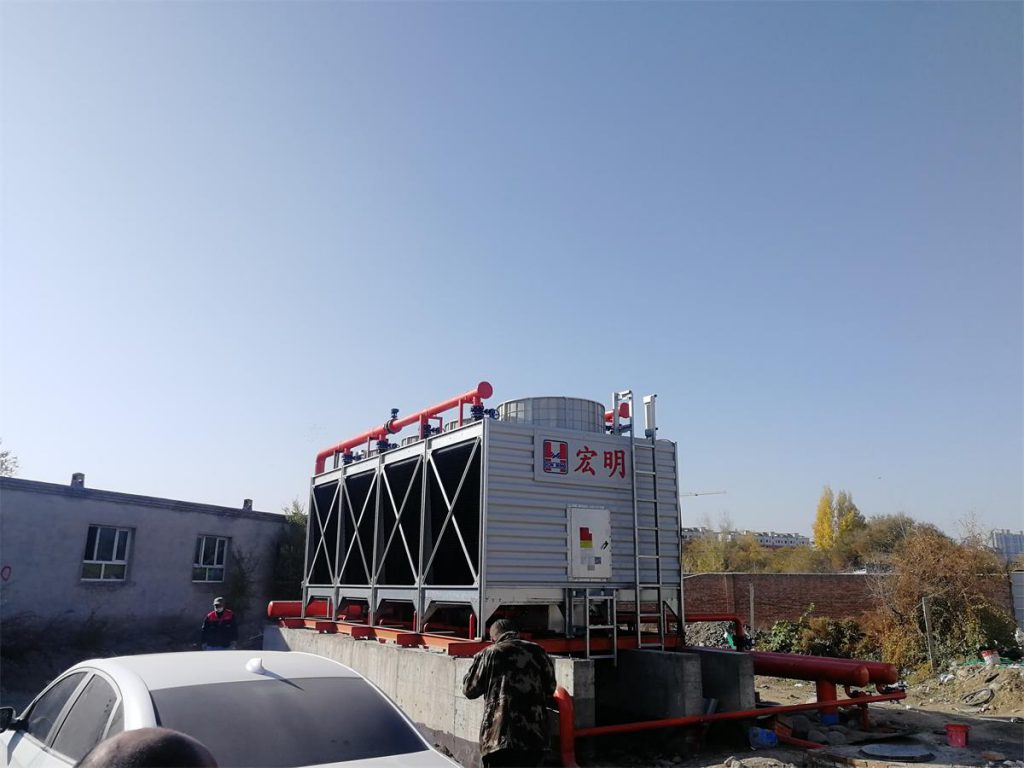
1. Scaling and Mineral Deposits: The Silent Efficiency Killer
The Problem:
Scaling occurs when minerals, especially calcium and magnesium, accumulate on heat exchange surfaces. Hard water intensifies this problem, reducing heat transfer efficiency and increasing energy costs.
The Solution:
- Install Water Softeners: Reduces mineral content before water enters the system.
- Use Anti-Scaling Chemicals: Specialized treatments prevent scale buildup.
- Routine Descaling: Schedule regular cleaning to remove existing scale.
Pro Tip:
Consider acid cleaning for severe scale buildup, but always consult with a professional to avoid damaging system components.
2. Corrosion: The Hidden Structural Threat
The Problem:
Moist environments and chemical imbalances can corrode metal components, compromising structural integrity and causing leaks or system failures.
The Solution:
- Water Treatment Programs: Balance water chemistry to control pH and prevent corrosion.
- Use Corrosion-Resistant Materials: Opt for stainless steel or fiberglass components.
- Apply Protective Coatings: Anti-corrosion coatings can shield vulnerable parts.
Pro Tip:
Install cathodic protection systems to mitigate corrosion in metal components, especially in aggressive environments.
3. Biological Growth: Algae, Mold, and Bacteria
The Problem:
Warm, moist conditions in cooling towers are ideal for algae, mold, and bacteria, including harmful Legionella bacteria, which can cause serious health risks.
The Solution:
- Regular Biocide Treatments: Rotate between oxidizing and non-oxidizing biocides to prevent resistance.
- UV Sterilization: Use UV light systems to kill bacteria without chemicals.
- Keep the Tower Clean: Remove debris and organic matter to discourage growth.
Pro Tip:
Install drift eliminators to minimize water vapor emissions, reducing the risk of airborne bacteria.
4. Mechanical Failures: Fans, Motors, and Pumps
The Problem:
Mechanical components like fans, motors, and pumps are prone to wear and tear, leading to vibration, noise, and reduced performance.
The Solution:
- Routine Inspections: Check for wear, misalignment, and lubrication issues.
- Predictive Maintenance: Use sensors to monitor vibration and temperature for early failure detection.
- Replace Worn Parts: Swap out aging bearings, belts, and seals promptly.
Pro Tip:
Upgrade to variable frequency drives (VFDs) to reduce mechanical stress and energy use by adjusting fan speeds according to demand.
5. Poor Water Distribution: Uneven Cooling
The Problem:
Clogged or misaligned nozzles can result in poor water distribution, leading to uneven cooling and reduced efficiency.
The Solution:
- Clean or Replace Nozzles: Regularly inspect and clean spray nozzles to ensure even distribution.
- Check Water Pressure: Maintain proper pressure for consistent spray patterns.
- Install Advanced Distribution Systems: Modern designs improve water flow and cooling performance.
Pro Tip:
Consider self-cleaning nozzles that reduce maintenance and prevent clogging.
6. Excessive Drift Loss: Water and Energy Waste
The Problem:
Drift loss occurs when water droplets escape with exhaust air, wasting water and spreading contaminants.
The Solution:
- Install High-Efficiency Drift Eliminators: Capture and return water droplets to the system.
- Optimize Fan Speed: Lower speeds reduce the force pushing water out of the tower.
- Maintain Fill Media: Clean and maintain fill material to improve airflow and reduce drift.
Pro Tip:
Use low-drift technology to cut water loss by up to 0.0005% of circulating water flow.
7. Insufficient Airflow: Reduced Heat Dissipation
The Problem:
Blocked air intakes, damaged fans, or poor ventilation can limit airflow, reducing heat removal efficiency.
The Solution:
- Clear Obstructions: Remove debris around air intakes and exhausts.
- Inspect and Repair Fans: Fix damaged blades and balance fans to ensure smooth operation.
- Upgrade Fan Systems: Replace aging fans with energy-efficient, high-performance models.
Pro Tip:
Install variable speed fans to optimize airflow based on real-time cooling demands.
8. Freezing in Cold Weather: A Seasonal Challenge
The Problem:
In colder climates, water inside the cooling tower can freeze, damaging components and halting operations.
The Solution:
- Install Basin Heaters: Prevent water in the basin from freezing.
- Use Variable Flow Systems: Adjust water flow to prevent stagnant, freezing water.
- Drain Idle Systems: When not in use, drain water to prevent ice buildup.
Pro Tip:
Install wind baffles to reduce wind chill effects and minimize freezing risks.
9. Overflow and Water Leaks: Wasted Resources
The Problem:
Leaky basins or malfunctioning overflow systems can waste water and damage equipment.
The Solution:
- Seal Leaks Promptly: Use industrial-grade sealants for small leaks.
- Inspect Overflow Systems: Ensure proper operation of float valves and overflow outlets.
- Upgrade Basin Materials: Switch to corrosion-resistant basins to prevent leaks.
Pro Tip:
Install automated water level controls to maintain optimal water levels and prevent overflow.
10. Noise Pollution: Disturbance and Compliance Risks
The Problem:
Cooling towers can generate excessive noise from fans, motors, and water flow, leading to regulatory issues and community complaints.
The Solution:
- Install Noise Dampeners: Use sound-absorbing materials and mufflers.
- Use Low-Noise Fans: Upgrade to quieter, aerodynamic fan blades.
- Optimize Water Flow: Adjust water distribution to minimize splashing sounds.
Pro Tip:
Install sound barriers or acoustic enclosures for noise-sensitive areas.
Conclusion: Proactive Maintenance = Peak Performance
Most cooling tower problems are preventable with proactive maintenance and timely upgrades. Addressing issues like scaling, corrosion, biological growth, and mechanical failures not only ensures efficient operation but also extends your system’s lifespan and saves on energy costs.
By implementing modern solutions—such as variable speed drives, advanced water treatments, and predictive maintenance tools—you can turn your cooling tower into a model of efficiency and reliability.
Stay ahead of common cooling tower problems, and your system will reward you with optimal performance and substantial energy savings.
Keywords: cooling tower problems, cooling tower maintenance, cooling tower solutions, industrial cooling efficiency, prevent cooling tower failure