Introduction
Cooling tower fillers play a crucial role in enhancing the heat exchange efficiency of a cooling system. Over time, these fillers deteriorate due to exposure to water, chemicals, and environmental factors. Replacing cooling tower fillers is essential for maintaining optimal performance, but understanding the associated costs is vital for budgeting and operational efficiency. This article provides a comprehensive guide to calculating the cost of replacing cooling tower fillers.
Factors Affecting Cooling Tower Filler Replacement Cost
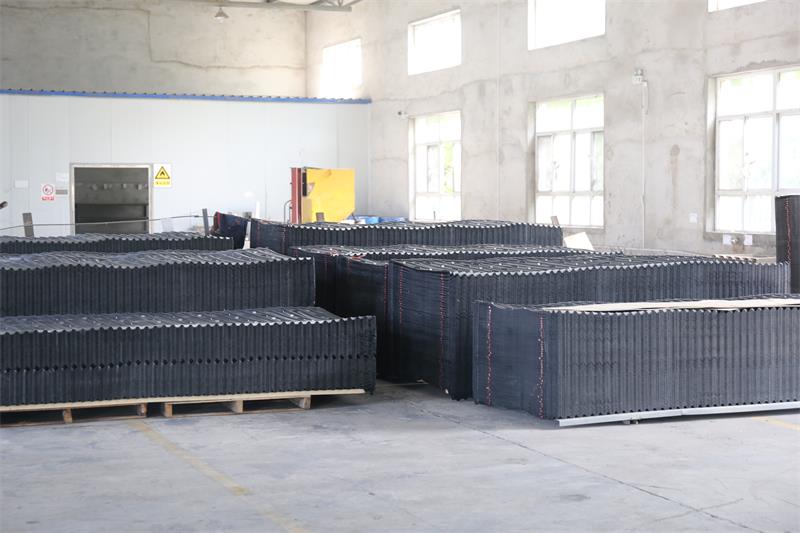
1. Type of Filler Material
Cooling tower fillers come in various materials, including PVC, polypropylene, and wood. The cost of these materials varies significantly:
- PVC Fillers: Most commonly used due to durability and cost-effectiveness.
- Polypropylene Fillers: More expensive but offer higher resistance to chemicals and extreme temperatures.
- Wood Fillers: Less common, often used in older towers, requiring specialized maintenance.
2. Size of the Cooling Tower
The size and capacity of the cooling tower determine the amount of filler material required. Larger cooling towers require more fillers, increasing both material and labor costs.
3. Labor Costs
Installation costs depend on labor rates, which vary by region. Skilled technicians are required for proper installation, ensuring efficiency and longevity.
4. Removal and Disposal Fees
The cost of removing and disposing of old fillers should be considered. Disposal fees depend on the type of material and local regulations regarding waste management.
5. Downtime Costs
Replacing fillers may require shutting down the cooling tower temporarily. The cost of downtime depends on the industry and the impact of reduced cooling capacity on operations.
6. Additional Maintenance or Repairs
If additional repairs or maintenance are required during filler replacement, these costs should be included in the overall budget.
Cost Calculation Formula
To estimate the total cost of cooling tower filler replacement, use the following formula:
Total Cost = (Filler Material Cost × Quantity) + Labor Cost + Removal & Disposal Fees + Downtime Cost + Additional Maintenance Costs
Example Calculation
Assume a cooling tower requires 500 square feet of PVC filler at $5 per square foot. Labor costs are estimated at $2,000, disposal fees at $500, and downtime costs at $1,500.
Total Cost = (500 × $5) + $2,000 + $500 + $1,500
Total Cost = $2,500 + $2,000 + $500 + $1,500 = $6,500
Conclusion
Understanding the cost components of cooling tower filler replacement helps businesses plan their budgets effectively. By considering material, labor, removal, downtime, and additional maintenance, companies can make informed decisions to optimize cooling tower performance while managing expenses efficiently.