Cooling towers play a crucial role in industrial and HVAC systems by dissipating excess heat through the process of evaporative cooling. This article provides an in-depth look at cooling towers, including their types, structure, parameters, and the key factors affecting their pricing.
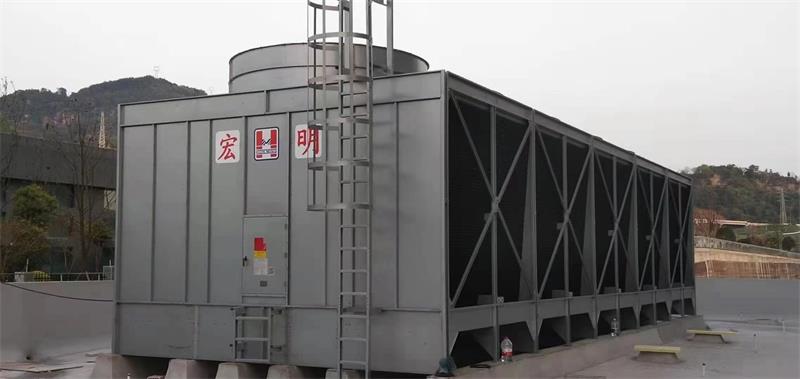
1. Introduction to Cooling Towers
A cooling tower is a heat dissipation device that uses water as a circulating coolant to absorb heat from a system and release it into the atmosphere. The cooling process occurs through heat exchange between water and air, where evaporation, convection, and radiation contribute to the cooling effect.
Cooling towers are widely used in industrial applications and HVAC (Heating, Ventilation, and Air Conditioning) systems to regulate water temperature, ensuring efficient operation of equipment. Due to their typical cylindrical or tower-like design, they are commonly referred to as “cooling towers.”
These towers integrate principles from multiple disciplines, including aerodynamics, thermodynamics, fluid mechanics, chemistry, material science, and structural mechanics. The cooling process is influenced by multiple factors and variables, making it a complex yet highly efficient cooling solution.
2. Cooling Tower Parameters
Cooling towers are categorized based on their cooling capacity and temperature drop efficiency. The following are standard temperature parameters for different cooling tower types:
Cooling Tower Type | Inlet Water Temperature (°C) | Outlet Water Temperature (°C) |
---|---|---|
Standard Type | 37°C | 32°C |
Medium-Temperature Type | 43°C | 33°C |
High-Temperature Type | 60°C | 35°C |
Ultra-High Temperature Type | 90°C | 35°C |
Large Cooling Towers | 42°C | 32°C |
The efficiency of a cooling tower is largely determined by temperature difference (∆T) and the ability to maintain optimal wet-bulb temperature conditions in different environments.
3. Cooling Tower Structure
A cooling tower is composed of several essential components, each playing a vital role in the cooling process:
Key Structural Components:
- Fill Media (Heat Exchange Material) → Enhances surface area for heat dissipation.
- Water Distribution System → Ensures uniform water distribution over the fill media.
- Ventilation Equipment (Fans and Motors) → Facilitates air circulation for evaporative cooling.
- Air Distribution System → Includes air intake louvers, guiding devices, and fan ducts to optimize airflow.
- Drift Eliminators (Water Droplet Collectors) → Reduces water loss by capturing airborne droplets.
- Cold Water Basin (Water Collection Tank) → Collects cooled water for recirculation.
These structural elements vary across different cooling tower designs, affecting efficiency, performance, and pricing.
4. Types of Cooling Towers
Cooling towers can be classified based on ventilation method, heat exchange mechanism, air-water flow direction, application type, noise levels, and shape.
4.1 By Ventilation Method
- Natural Draft Cooling Tower → Utilizes natural airflow without mechanical fans.
- Mechanical Draft Cooling Tower → Uses fans to enhance airflow and cooling efficiency.
- Hybrid Ventilation Cooling Tower → A combination of natural and mechanical ventilation.
4.2 By Heat Exchange Mechanism
- Wet Cooling Tower → Relies on evaporative cooling (most common type).
- Dry Cooling Tower → Uses heat exchangers without water evaporation.
- Dry-Wet Hybrid Cooling Tower → A mix of wet and dry cooling for optimized efficiency.
4.3 By Air and Water Flow Direction
- Counterflow Cooling Tower → Water flows downward while air moves upward.
- Crossflow (Horizontal Flow) Cooling Tower → Water flows vertically while air moves horizontally.
- Mixed Flow Cooling Tower → A hybrid of counterflow and crossflow designs.
4.4 By Application
- Industrial Cooling Tower → Used in power plants, chemical plants, and manufacturing.
- HVAC Cooling Tower → Supports air conditioning systems in commercial buildings.
4.5 By Noise Level
- Standard Noise Cooling Tower → Regular noise levels.
- Low-Noise Cooling Tower → Includes noise-reduction features.
- Ultra-Low Noise Cooling Tower → Designed for environments with strict noise regulations.
- Super Silent Cooling Tower → Equipped with advanced soundproofing materials.
4.6 By Shape
- Round Cooling Tower → Cylindrical structure, common for smaller systems.
- Square Cooling Tower → Space-efficient design for large-scale applications.
- Other Designs → Includes jet cooling towers, fanless cooling towers, and modular cooling towers.
5. Factors Affecting Cooling Tower Prices
The cost of a cooling tower varies based on multiple technical and environmental factors. Below are the primary price determinants:
5.1 Size and Capacity
- Larger cooling towers with higher flow rates cost more due to increased material and construction costs.
- Heat exchange area directly impacts performance and pricing.
5.2 Fan & Motor Brand
- Premium fan and motor brands offer greater energy efficiency and durability but come at a higher cost.
- Explosion-proof motors (used in hazardous environments) increase costs.
5.3 Heat Exchange Efficiency & Pipe Quality
- Seamless pipes vs. Welded pipes:
- Seamless pipes → Higher durability, better heat transfer, but more expensive.
- Welded pipes → More affordable but lower efficiency.
- Pipe wall thickness → Thicker pipes improve durability but increase costs.
5.4 Energy Efficiency & Operating Costs
- High-efficiency cooling towers reduce long-term energy expenses but may have higher initial costs.
- Systems with variable speed drives (VSDs) or EC motors enhance energy savings.
5.5 Cooling Load & Temperature Parameters
- Cooling towers must be custom-designed for specific applications.
- A 100-ton cooling tower in different wet-bulb temperatures requires different sizing and pricing.
5.6 Wet-Bulb Temperature & Location
- Geographic location impacts cooling efficiency:
- Hotter climates require larger cooling towers.
- Humid regions demand better airflow and heat dissipation designs.
5.7 Materials & Corrosion Resistance
- Stainless steel & FRP (Fiberglass Reinforced Plastic) cooling towers offer better corrosion resistance but are pricier.
- Galvanized steel options are more affordable but may degrade faster in harsh environments.
5.8 Additional Custom Features
- Soundproofing materials for noise reduction.
- Anti-freeze systems for cold climate applications.
- Fire-resistant coatings for industrial safety compliance.
5.9 Manufacturer & Certification
- Reputable brands with ISO, AHRI, or CTI certifications typically charge more but offer better performance and longevity.
- On-site factory visits and performance tests help verify product quality before purchase.
6. Conclusion
Cooling tower prices depend on technical specifications, efficiency, materials, and location-specific factors. To get an accurate price estimate, you should provide details such as:
- Flow rate (m³/h or GPM)
- Temperature drop required (∆T)
- Wet-bulb temperature of the location
- Application type (HVAC or industrial use)
By understanding these factors, you can select the right cooling tower that balances cost, performance, and energy efficiency for your project. 🚀