Closed-circuit cooling towers can be categorized based on their cooling principles into counterflow, parallel flow, crossflow, wastewater, hybrid, and integrated heat exchange stations. Each has a distinct structural design and operating mechanism.
1️⃣ Counterflow Closed-Circuit Cooling Tower
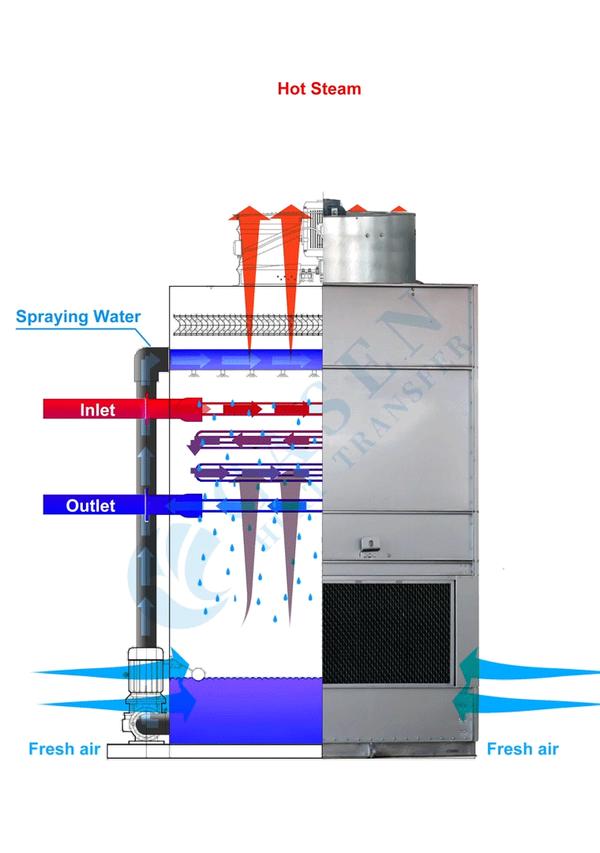
🔹 Working Principle:
- The working fluid circulates within the coil inside the tower.
- Heat from the working fluid transfers through the coil walls to the sprayed water outside.
- A fan draws in air from the bottom, moving upward in the opposite direction to the water flow.
- Some water evaporates, absorbing heat and forming warm humid air, which is discharged at the top.
- The remaining water collects at the bottom and is recirculated by a pump.
📌 Key Feature: Efficient counterflow heat exchange maximizes cooling performance.
2️⃣ Parallel Flow Closed-Circuit Cooling Tower
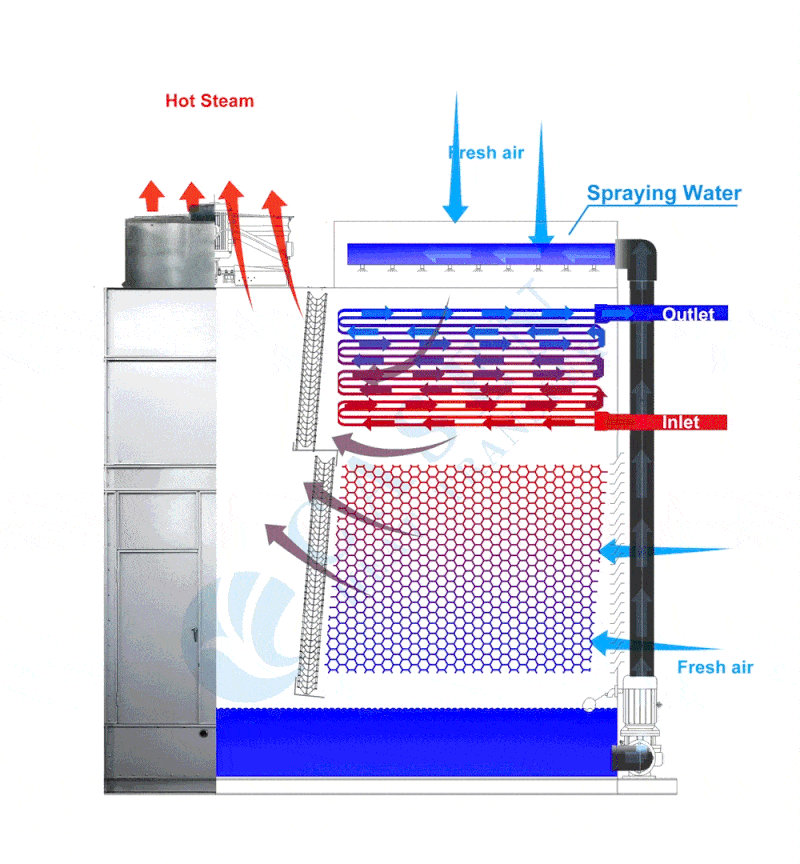
🔹 Working Principle:
- The working fluid (water, oil, or other liquids) flows inside the coil, while spray water surrounds the coil externally.
- Heat transfers from the fluid to the water and air, forming saturated hot steam.
- A fan expels the heat into the atmosphere, while the water droplets are collected and recirculated.
- Spray water is cooled through PVC heat exchange panels before being reused.
- The airflow and water flow move in the same direction (parallel flow), reducing scaling on the coil walls.
📌 Best For: High-temperature fluids (~60°C) or large cooling differentials (e.g., 60°C → 35°C).
3️⃣ Hybrid Closed-Circuit Cooling Tower
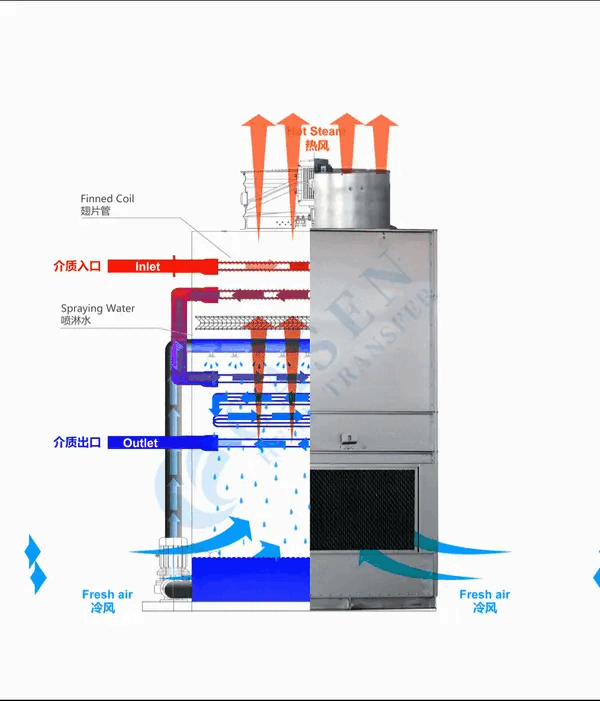
🔹 Working Principle:
- The working fluid first passes through a finned coil unit located above the demister and below the fan.
- The first cooling stage: Sensible heat is dissipated from the finned coil to the air, reducing the thermal load on the main coil section.
- The second cooling stage: Spray water flows over the main coil, allowing latent and sensible heat exchange.
- The remaining heat is expelled through the fan, while un-evaporated water collects and recirculates.
📌 Key Feature: Pre-cooling via the finned coil reduces evaporation losses and increases efficiency.
4️⃣ Crossflow Closed-Circuit Cooling Tower
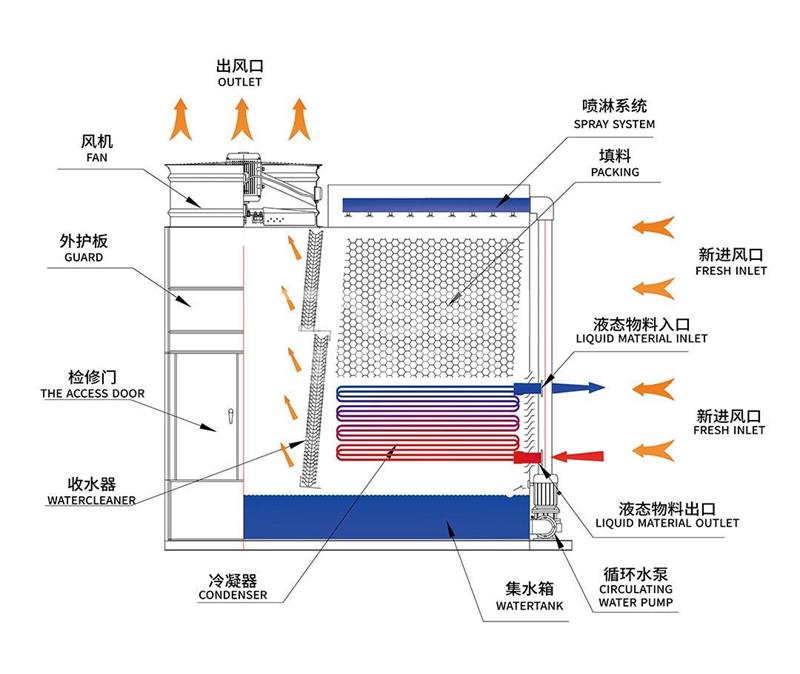
🔹 Working Principle:
- The working fluid flows inside the coil, while spray water surrounds it externally.
- Heat is transferred from the fluid to the spray water and air, forming hot vapor.
- The fan expels the heat, while a collection system prevents water loss.
- The air enters laterally (from the sides) and moves horizontally across the sprayed water, promoting efficient heat exchange.
- PVC heat exchange panels further reduce water temperature before recirculation.
📌 Best For: Applications with strict noise requirements and moderate temperature differentials (ΔT = 4-15°C), such as air conditioning and industrial processes.
5️⃣ Integrated Dry-Wet Hybrid Heat Exchange Station
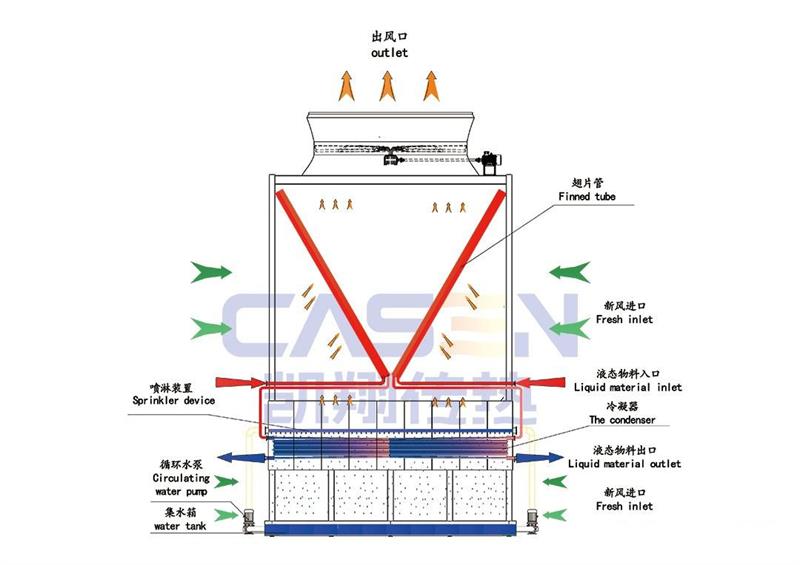
🔹 Working Principle:
- A typical integrated hybrid cooling system consists of an air-cooling tower and an evaporative cooling tower connected in series.
- Stage 1 (Dry Cooling):
- Hot process water first enters the air-cooled section, where ambient air cools the water via finned tubes.
- Stage 2 (Wet Cooling):
- The semi-cooled water then enters the evaporative section, where it undergoes further cooling via sprayed water and evaporative heat exchange.
- Metallic heat exchangers (such as stainless steel tubes or aluminum fins) improve heat transfer efficiency.
📌 Key Feature: Combines dry and wet cooling for enhanced efficiency and reduced water consumption.
6️⃣ Wastewater Closed-Circuit Cooling Tower
🔹 Working Principle:
- Specifically designed for industries handling contaminated, viscous, or high-fouling fluids.
- Uses detachable heat exchanger designs (e.g., removable plate-type or cap-style heat exchangers) for easy maintenance.
- Ideal for fluids with high scaling tendencies (thermal resistance > 0.00034 m²·K/W) or where chemical cleaning is ineffective.
📌 Best For: Sewage treatment plants, heavy industry, and process industries handling high-fouling liquids.
🔹 Summary: Choosing the Right Closed-Circuit Cooling Tower
Cooling Tower Type | Air & Water Flow Direction | Best For | Key Feature |
---|---|---|---|
Counterflow | Air upward, water downward | General cooling applications | Maximizes heat exchange efficiency |
Parallel Flow | Air and water flow in the same direction | High-temperature fluids, large ΔT (60°C → 35°C) | Reduces coil scaling |
Hybrid | Two-stage cooling with finned coil + spray coil | High-load industrial cooling | Pre-cooling reduces evaporation loss |
Crossflow | Air horizontal, water vertical | Noise-sensitive areas, HVAC | Quiet operation, moderate cooling loads |
Integrated Dry-Wet | Series cooling (air + evaporative cooling) | Energy-efficient cooling, low water consumption | Combines dry and wet cooling for efficiency |
Wastewater Cooling Tower | Custom designs for fouling fluids | Heavy industry, sewage plants | Special anti-scaling design |
Conclusion
✅ Different closed-circuit cooling towers suit different cooling requirements.
✅ Counterflow and crossflow towers are common in HVAC and industrial cooling.
✅ Parallel flow towers are best for high-temperature fluids.
✅ Hybrid and integrated dry-wet towers improve efficiency and water savings.
✅ Wastewater towers are designed for contaminated or high-fouling liquids.
🔹 Choosing the right type depends on factors like temperature differential (ΔT), noise constraints, water quality, and operational efficiency.
👉 Now you know how different closed-circuit cooling towers work! 😊