How to Calculate Cooling Tower Capacity Requirements
Cooling towers play a crucial role in removing excess heat from industrial processes, HVAC systems, and power plants. Properly sizing a cooling tower is essential for optimal performance, energy efficiency, and equipment longevity. In this guide, we’ll explain the key factors involved in calculating cooling tower capacity requirements to help you select the right system for your needs.
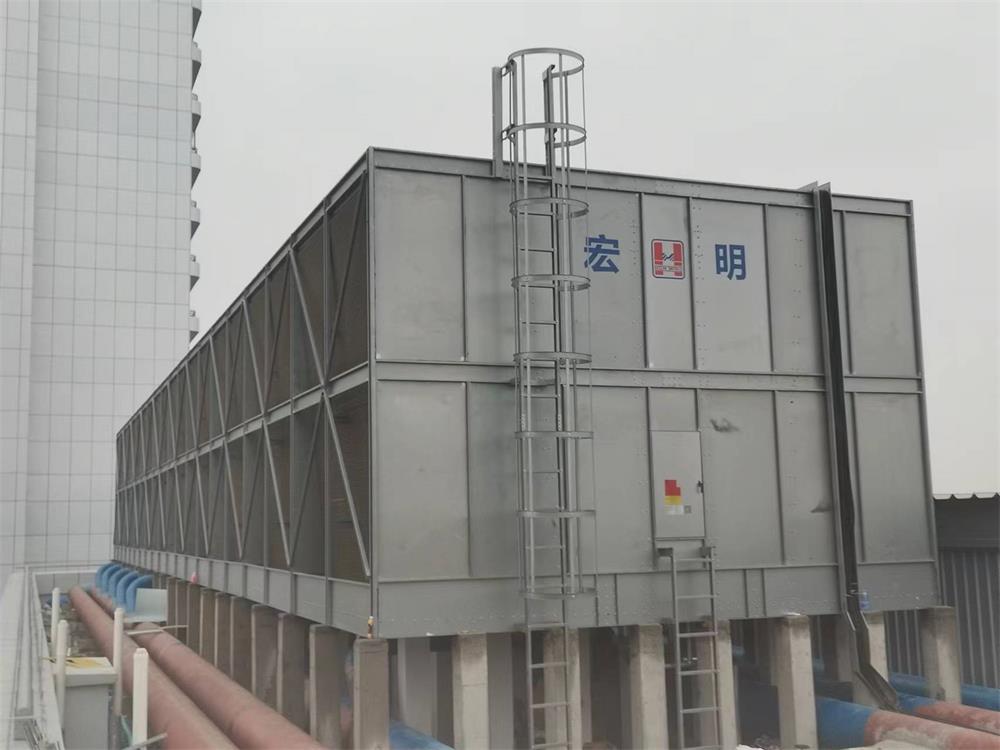
1. Understanding Cooling Tower Capacity
Cooling tower capacity is measured in tons of refrigeration (TR) or British Thermal Units per hour (BTU/h). One ton of cooling is equal to 12,000 BTU/h or the amount of heat required to melt one ton of ice in 24 hours.
The formula to determine cooling tower capacity is:
Q=500×GPM×ΔT/12,000
Where:
- Q = Cooling tower capacity (tons)
- GPM = Water flow rate (gallons per minute)
- ΔT = Temperature difference (°F) between hot and cold water
- 500 = A constant that accounts for the specific heat of water
2. Key Factors in Cooling Tower Sizing
A. Heat Load Calculation
The heat load is the total amount of heat energy that must be removed from a system. It depends on process requirements, equipment specifications, and ambient conditions.
The formula for heat rejection:
Q=500×GPM×(T_hot−T_cold)
Where:
- T_hot = Temperature of the hot water entering the cooling tower
- T_cold = Temperature of the cooled water exiting the cooling tower
For example, if a system circulates 1,000 GPM of water and cools it from 95°F to 85°F, the required cooling tower capacity would be:
Q=500×1,000×(95−85)/12,000=416.7 tons
B. Wet Bulb Temperature Consideration
The wet bulb temperature (WBT) is a critical factor in cooling tower performance. It represents the lowest temperature water can reach through evaporative cooling. Cooling towers typically achieve an approach of 5-10°F above the wet bulb temperature.
If the WBT is 75°F and the desired cold water temperature is 85°F, the approach temperature is:
85°F – 75°F = 10°F
A lower approach temperature requires a larger cooling tower.
C. Evaporation and Drift Losses
- Evaporation Loss: For every 1°F of cooling, approximately 0.0015 gallons per minute (GPM) per ton of water evaporates.
- Blowdown Loss: To prevent scaling and contamination, some water must be discharged and replaced with fresh water.
- Drift Loss: Tiny water droplets carried away with exhaust air, typically 0.002% to 0.005% of the circulating water.
3. Step-by-Step Cooling Tower Sizing Example
Example Scenario:
A facility needs to cool 1,200 GPM of water from 95°F to 85°F in an area with a 78°F wet bulb temperature.
Step 1: Calculate Required Capacity
Q=500×1,200×(95−85)/12,000=500 tons
Step 2: Consider Approach Temperature
85°F−78°F=7°F
Since the approach is within the typical 5-10°F range, the system is feasible.
Step 3: Estimate Water Losses
- Evaporation Loss:
0.0015×500=0.75 GPM - Drift & Blowdown Losses: Estimated at 20% of evaporation loss
0.75×1.2=0.9 GPM
Total water loss: 1.65 GPM
4. Choosing the Right Cooling Tower
When selecting a cooling tower, consider:
- Type: Crossflow vs. Counterflow, Induced Draft vs. Forced Draft
- Efficiency: Higher efficiency towers reduce operating costs
- Footprint: Available installation space
- Environmental Conditions: Humidity, altitude, and water quality
Conclusion
Accurately calculating cooling tower capacity is essential for efficient operation and cost savings. By considering heat load, wet bulb temperature, and water losses, you can select the optimal cooling tower for your application. If you’re unsure about your specific requirements, consulting a professional can help optimize your cooling system performance.
Would you like help selecting the best cooling tower for your facility? Contact us today!